Przebudowa maszyny serwetkowej oraz wymiana przestarzałego systemu sterowania i bezpieczeństwa na najnowsze rozwiązania.
Projekt obejmował modernizację maszyny do produkcji serwetek. Wymianie podlegał cały układ sterowania wraz z szafami sterowniczymi, jak również modernizacja mechaniczna maszyny. Dzięki modernizacji nastąpiła poprawa bezpieczeństwa, wydajności, diagnostyki i powtarzalności produkcji na maszynie.
Ze względu na wielkość, projekt został podzielony na kilka etapów: inwentaryzacja stanu obecnego, opracowanie koncepcji, przygotowanie projektów mechanicznych i elektrycznych, kompletacja podzespołów, demontaż, montaż, uruchomienie i asysta produkcyjna.

Założenia i wyzwania projektu
- Brak dokumentacji technicznej maszyny i związana z tym konieczność pełnej inwentaryzacji maszyny.
- Trudna serwisowalność obecnej maszyny ze względu na coraz trudniej dostępne, lub wręcz niedostępne na rynku części zamienne oraz ze względu na bardzo słabą diagnostykę.
- Nie spełnianie przez maszynę wymogów bezpieczeństwa – konieczność modernizacji całego systemu bezpieczeństwa i dostosowanie go do obowiązujących norm i dyrektyw.
- Maszyna była jedyną na zakładzie, która produkowała specyficzny asortyment dla kluczowego klienta – modernizacja musiała być przeprowadzona sprawnie.
- Zastosowanie niezbędnych czujników w celu poprawienia dokładności i diagnostyki.
- Wymiana części mechanicznych – wałków, podestów, osłon… mimo braku dokumentacji rysunkowej.
- Maszyna jest wykorzystywana w ciągłej produkcji 24/7 z bardzo dużą wydajnością, wymagała więc precyzyjnego wykonania mechanicznego i niezawodnego systemu sterowania.
- Maszyna dotąd była napędzana jednym silnikiem, łańcuchem wraz z niezliczoną ilością przekładni i kół zębatych, musiało to zostać zastąpione osobnymi osiami napędzanymi przez silniki serwo.
- Ułatwienie obsługi wałków „sleeve”, aby mogły być wymieniane przez jednego operatora, a nie dwóch jak dotąd.
Korzyści z projektu
- Odtworzenie dokumentacji maszyny.
- Spełnienie norm bezpieczeństwa i zapewnienie operatorom bezpiecznej pracy.
- Zaprojektowanie nowych zamków dla wymiany wałków „sleeve”, aby wymiany wałków dokonywał jeden operator.
- Nowoczesny system sterowania z pełną dostępnością części zamiennych.
- Niezależna praca napędów – brak wpływu zmian długości łańcuch na jakość i dokładność pracy maszyny.
- Pełna diagnostyka błędów i awarii.
- Mniej odrzutu produktu podczas startu maszyny.
- Zapewnienie odpowiedniego poziomu hałasu generowanego przez maszynę.
- Lepsza ergonomia obsługi maszyny.
Etap 0 | Koncepcja i inwentaryzacja
Realizacja projektu rozpoczęła się od, wspólnego z klientem, wypracowania koncepcji całej modernizacji. Klient miał bardzo duże doświadczenie jeśli chodzi o tego typu maszyny, bo w swoim parku maszynowym posiadał ich znacznie więcej, niektóre starsze, a niektóre całkiem nowe. Wiedział więc doskonale czego chce, co mu odpowiada, a jakich rozwiązań chciałby unikać.
Kiedy wstępna koncepcja została wypracowana rozpoczęliśmy najtrudniejszy etap realizacji, czyli inwentaryzację – musieliśmy pomierzyć wszystkie części maszyny i spisać wszystkie elementy.
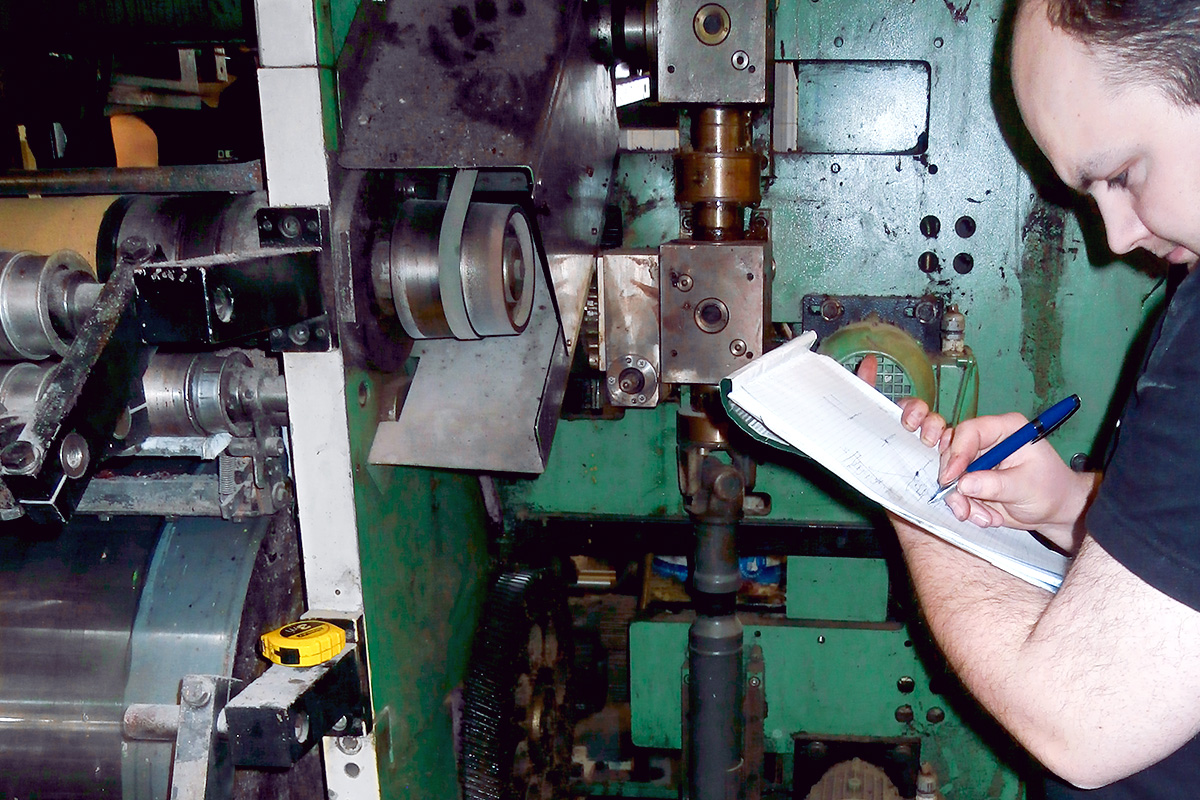

Etap 1 | Projekt
Mając za sobą etap inwentaryzacji rozpoczęło się projektowanie – zarówno mechaniczne jak i to związane z systemem sterowania. Praca konstruktorska wymagała przeprojektowania wielu elementów maszyny, przygotowania do niej nowych podestów obsługowych, osłon itp., uwzględniając przy tym zapewnienie odpowiedniego poziomu bezpieczeństwa, hałasu i ergonomii obsługi. Układ sterowania niejako nadążał za konstrukcją dostosowując się do jej potrzeb. Ponieważ park maszynowy klienta oparty był głównie na systemach sterowania Siemensa, my również zastosowaliśmy osprzęt tego producenta w naszym systemie. Aby sprostać wysokim wymaganiom prędkości i dokładności maszyny, wspólnie z naszym partnerem – firmą Siemens dobraliśmy układ sterowania, który gwarantował sprostanie wymogom maszyny.
Etap 2 | Kompletacja i montaż
Po procesie projektowania, rozpoczął się proces kompletacji dostaw i prefabrykacji.
Gdy byliśmy gotowi do rozpoczęcia prac na obiekcie, rozpoczął się najtrudniejszy okres z punktu widzenia klienta – trzeba było odstawić maszynę z produkcji, abyśmy mogli ją całkowicie rozebrać i zacząć budować od nowa. Był to oczywiście równie stresujący okres dla nas, bo zależało nam aby jak najszybciej wykonać swoją pracę, a wiadomo, że nawet najlepsza inwentaryzacja nie ustrzegła by nas przed błędami i problemami, które musieliśmy na bieżąco rozwiązywać, czasami wykonując niektóre części całkowicie od nowa. Na szczęście takich potknięć było niewiele i maszyna została złożona ponownie.
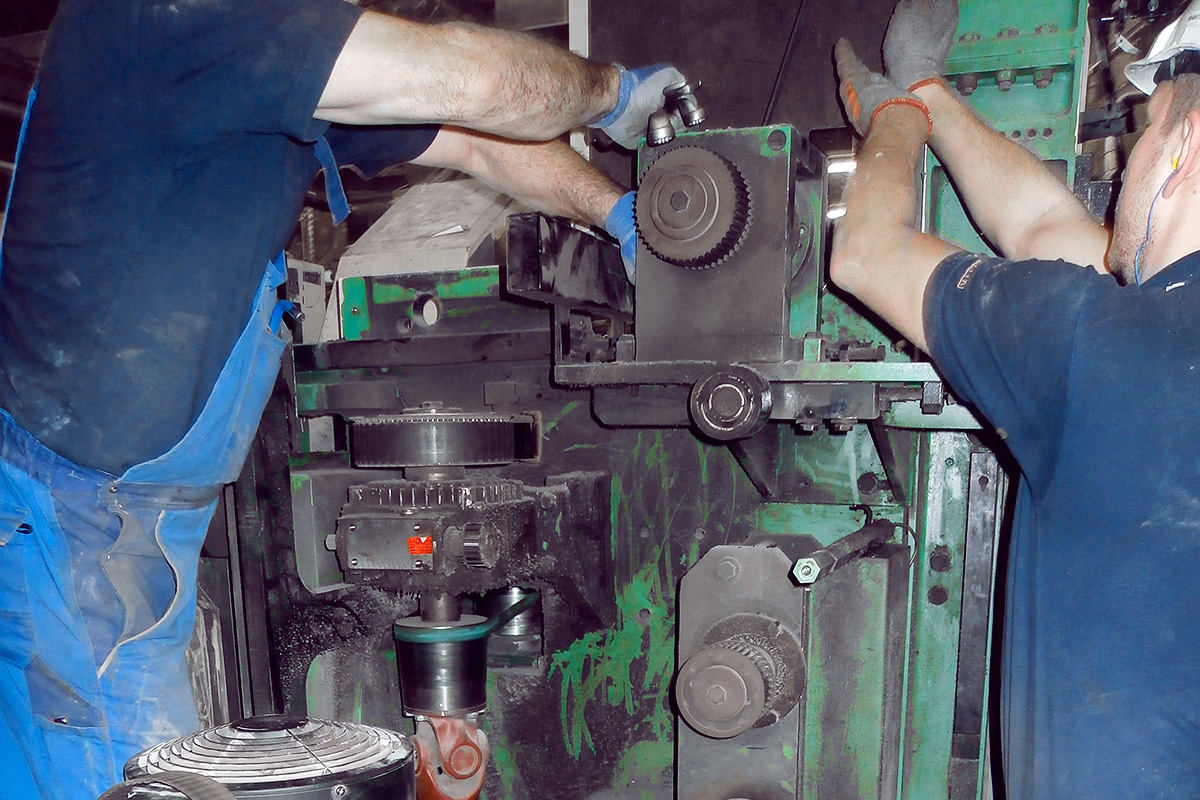
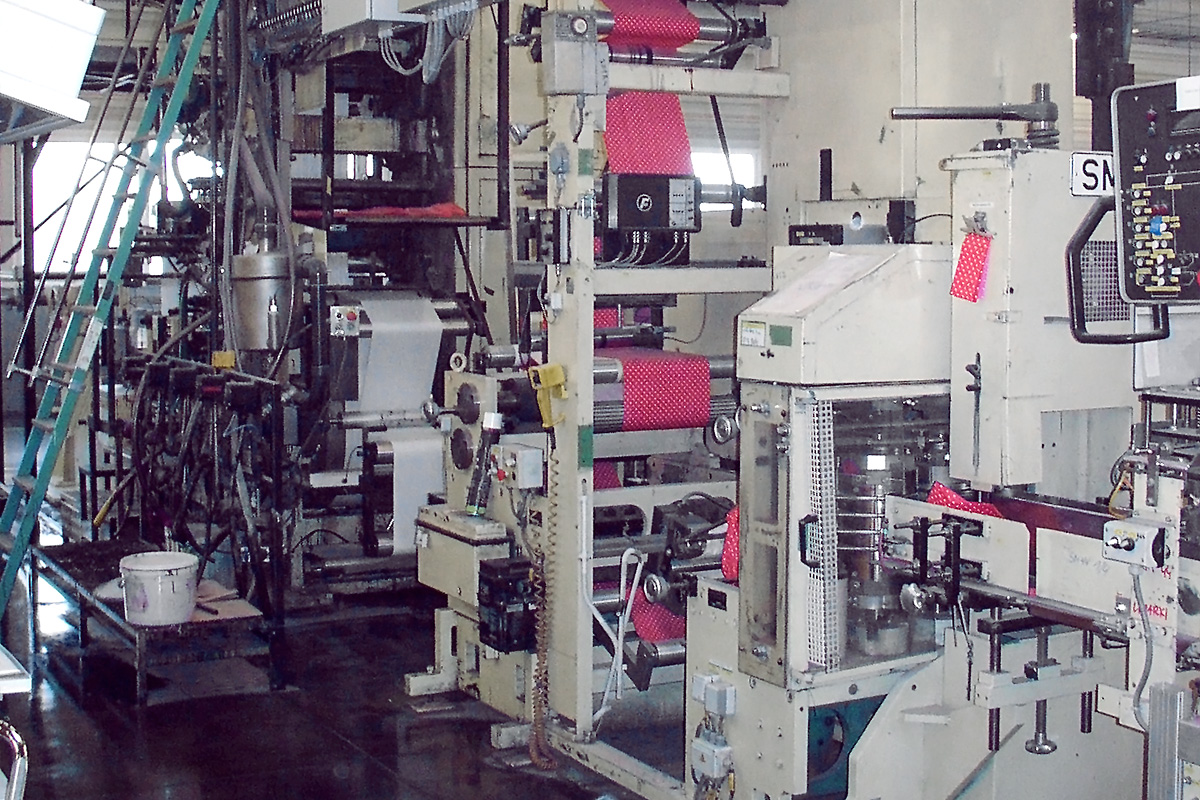
Etap 3 | Uruchomienie
Teraz rozpoczął się proces uruchamiania, który zawsze rozpoczynamy od dokładnego testu i/o, testu systemów bezpieczeństwa, potem przechodząc do testu poszczególnych urządzeń, a kończąc na teście pracy automatycznej. Ponieważ funkcjonalność maszyny została mocno przeprojektowana – choćby zamiast jednego napędu głównego napędzającego całą maszynę za pomocą łańcucha, powstało 20 niezależnych układów serwo, które musiały być sprzęgnięte tak aby wszystkie działały jak jeden mechanizm – testy i parametryzowanie zajęły sporo czasu, ale udało się osiągnąć efekt, który w pełni zadowalał naszego klienta.
Podsumowanie
Efektem naszej pracy jest „nowa” maszyna spełniająca wymogi klienta, a przede wszystkim produkująca produkt zadowalający odbiorcę końcowego, którą można łatwiej diagnozować, szybciej serwisować i przezbrajać oraz spełniająca obowiązujące wymogi bezpieczeństwa i higieny pracy. Zdobyliśmy dużą wiedzę w temacie prowadzenia bibuły, kontroli naciągu, pozycjonowania druku i procesu produkcji.
Ten krótki opis nie jest w stanie pokazać dokładnie jak dużym wyzwaniem był ten projekt i jak spektakularny efekt udało nam się uzyskać, ale jeśli jesteś zainteresowany modernizacją swoich maszyn to zapraszamy do kontaktu, odpowiemy na Twoje pytania, podzielimy się naszym doświadczeniem i spróbujemy rozwiązać Twoje problemy.
Zastosowane komponenty
- Sterownik Siemens S7-300 Fail-Safe
- System napędowy Simotion D
- Panele HMI Siemens 19”
- System wizyjny BST
- Prowadzenie wstęgi BST