Nowy system wizyjny do automatycznej kontroli jakości zainstalowany w obrębie pracującej już linii produkcyjnej w branży spożywczej.
Dla jednego z naszych stałych klientów przeprowadziliśmy unowocześnienie jednej z linii produkcyjnych, którego celem była optymalizacja procesu produkcji w obszarze kontroli jakości.
Cel ten został zrealizowany poprzez zainstalowanie nowego systemu wizyjnego do automatycznej kontroli jakości zgodnie z założeniami działu produkcji i kontroli jakości.
Zapraszamy do zapoznania się ze szczegółami w poniższym studium przypadków.

Główne założenia projektu
- Zaprojektowanie i zainstalowanie systemu wizyjnego zgodnie z wytycznymi działu produkcji i kontroli jakości.
- Odrzut określonej partii niewłaściwych produktów, odrzucenie jednego konkretnego rzędu spośród trzech.
- Detekcja wad zarówno od dołu, jak i od góry produktu przy uwzględnieniu kilku wariantów produktów o różnych cechach.
- Opracowanie optymalnych algorytmów dla założonych poziomów produkcji.
- Przystosowanie systemu do przenośnika o zmieniającej się dynamice posuwu oraz zmiennego układu produktów w trakcie procesu.
- Montaż systemu w dostępnej przestrzeni na linii produkcyjnej
Etap 0 | Przygotowanie do zlecenia
W etapie 0, przed otrzymaniem zlecenia, klient w pierwszej kolejności wybrał dostawcę urządzeń systemów wizyjnych, z którym przeprowadził wstępne testy, a następnie powierzył nam zaprojektowanie całej instalacji (w oparciu o dobrane przez klienta i dostawcę urządzenia) oraz opracowanie algorytmów do automatycznej kontroli jakości wg działku produkcji i kontroli jakości.
Przed rozpoczęciem prac ustaliliśmy z klientem miejsce instalacji, zrobiliśmy niezbędną inwentaryzację linii i przeprowadziliśmy pomiary potrzebne do zaprojektowania konstrukcji oraz dobrania odpowiedniego sterowania.
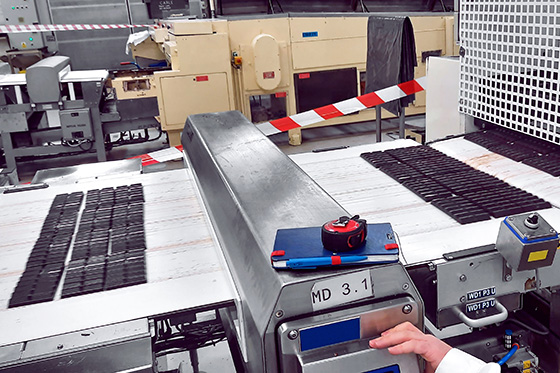
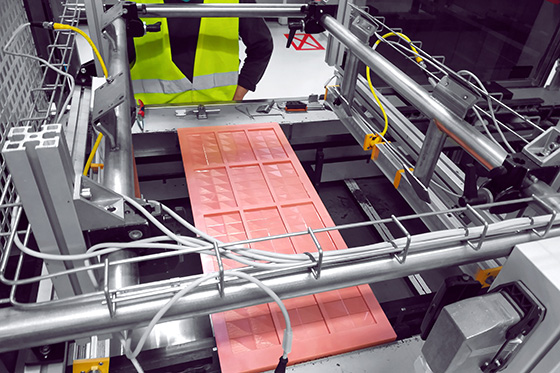
Etap 1 | Realizacja zlecenia
Realizację zlecenia rozpoczęliśmy od przedstawienia klientowi projektu konstrukcji, na której miały się znaleźć urządzenia systemu wizyjnego oraz systemu odrzutu. Ten moment był ważny, ponieważ konstrukcja miała spełniać wymogi klienta, tj. mobilna konstrukcja, która umożliwiłaby przeprowadzenie prac serwisowych i konserwacyjnych bez zakłócenia produkcji.
Następnie po zaakceptowaniu przez klienta konstrukcji rozpoczął się proces kompletacji i prefabrykacji, zarówno konstrukcji, jak i systemu wizyjnego wraz z systemem sterowania. Kolejno mając już wszystkie elementy systemu, przeszliśmy do montażu instalacji i do urchomienia systemu.
Etap 2 | Testy przed wdrożeniem
Po zainstalowaniu i uruchomieniu całego systemu przeprowadziliśmy testy przed wdrożeniem, które niestety wykazały słabe punkty z pierwszych próby na etapie 0, które na tamten moment były trudne do przewidzenia. W związku z tym wykonaliśmy dodatkowe testy, aby znaleźć optymalne rozwiązanie. Między innymi sprawdziliśmy różne warianty umieszczenia oświetlaczy względem kamer i produktu, czy zastosowaliśmy różną konfigurację soczewek i dyfuzorów w kamerach. Ostatecznie dostawca dostarczył dodatkowe oświetlenie, które dały satysfakcjonujący efekt.

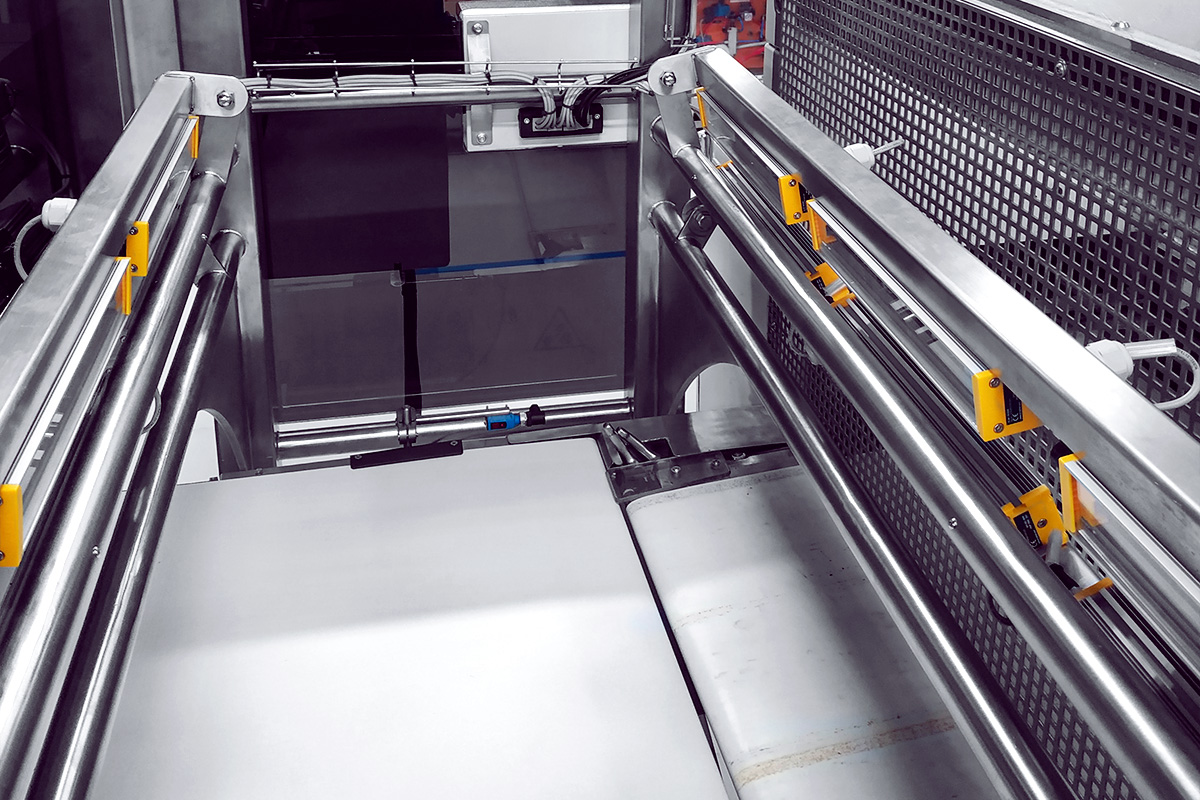
Etap 3 | Wnioski
Przy doborze oświetlenia systemu wizyjnego, szczególną uwagę należy zwrócić na równomierne oświetlenie, zarówno ilość światła, jak i umiejscowienie lamp. Rozmieszczenie lamp – położenie oraz kąt, należy wykonać w taki sposób, aby światło nie tworzyło refleksów, a uwypuklało defekty produktu. Przy tym projekcie było to trudne do osiągnięcia, ponieważ mierzyliśmy się z kilkoma wariantami produktów, które różniły się od siebie kształtem i poziomem refleksyjności. O ile dla każdego rodzaju produktu można przygotować oddzielny algorytm inspekcji, o tyle parametrów związanych ze światłem tak łatwo nie zmienimy, dlatego oświetlenie ma kluczowe znaczenie w takich systemach.
Etap 4 | Tworzenie algorytmów
Mając już odpowiednio przygotowane oświetlenie systemu wizyjnego przeszliśmy do fazy tworzenia algorytmów. Zespół inżynierów zrealizował założenia projektu i opracował algorytmy, które odrzucały określną partię niewłaściwych produktów (odrzucenie jednego konkretnego rzędu spośród trzech), uwzględniając detekcję wad zarówno od dołu produktu, jaki i od góry dla kilku wariantów produktów o różnych cechach. Możemy też się tutaj pochwalić, że system oraz algorytmy były na tyle dokładne, że wykrywały rzeczy niewidoczne dla oka – na szczęście nie miały wpływu na jakość samego produktu, a jedynie wskazują na czułość systemu.
Rezultaty projektu
Ostatecznie cała instalacja składała się z dwóch stanowisk systemu wizyjnego oraz stanowiska odrzutu. Pierwsze stanowisko systemu wizyjnego odpowiada za inspekcję dolnej części produktu. W tym miejscu produkt porusza się w taktach, dlatego inspekcję możemy wykonać statycznie. Jest to spore ułatwienie, gdyż produkt znajduje się w powtarzalnej pozycji. Dodatkowo możemy pozwolić sobie na dłuższy czas akwizycji zdjęcia (otwarcia migawki kamery). Kompensuje to kwestie niedostatecznego oświetlenia i nie stwarza ryzyka rozmazania obrazu. 13 taktów dalej znajduje się druga stacja systemu wizyjnego odpowiedzialna za inspekcję górnej strony produktu (pomiędzy stacjami produkt jest odwracany). Tutaj trudność stanowił fakt, że produkt nie poruszał się w tackach, tylko na przenośniku o dynamicznie zmieniającej się prędkości, oscylującej wokół wartości 0,5 m/s. Czas otwarcia migawki w tym przypadku wynosi tylko 0,8 ms, dlatego tak ważne okazało się odpowiednie oświetlenie produktu. Inspekcja każdej grupy produktów następuje w formie serii 3 zdjęć wykonywanych w odstępach ok. 140ms. Dynamiczna zmiana prędkości pasa wynikała ze specjalnie wypracowanego algorytmu zapewniającego rozdzielenie produktów od siebie. Sklejone produkty są bowiem trudne do zidentyfikowania przez system wizyjny.
Następnym wyzwaniem było zapewnienie prawidłowej korelacji danych pomiędzy pierwszą, a drugą stacją systemu wizyjnego. Algorytm został zabezpieczony w taki sposób, że nawet “ręczne” wyeliminowanie produktu pomiędzy dwoma stacjami nie zaburzało sekwencji analizy danych. Wszystkie dane zostają przesyłane do sterownika PLC, który odpowiada za odrzut 1, 2 lub 3 rzędów produktów. Pozycja każdego z 12 produktów wchodzących w skład 1 grupy produktów jest dokładnie mierzona z wykorzystaniem dalmierzy optycznych oraz informacji z enkodera serwonapędu. Następnie w przypadku zapewnienia odrzutu, produkt jest precyzyjnie zdmuchiwany z linii produkcyjnej.
Podsumowanie projektu
Dzięki zastosowaniu systemy wizyjnego do automatycznej kontroli jakości produktów zostało zoptymalizowane obsadzenie pracowników w dziale kontroli jakości (6 pracowników zostało przydzielonych do innych prac w zakładzie). Dodatkowo klient uzyskał mniejsze odpady oraz otrzymał określoną i powtarzalną jakość w produkcie końcowym.
Z naszej strony uzyskaliśmy zadowalające efekty dla klienta oraz zrealizowaliśmy założenia projektu. Jesteśmy dumni z tego, ponieważ projekt był mocno angażujący i pochłoną dużą liczbę godzin, ale zadowolenie klienta jest dla nas priorytetem i to nas cieszy. Nagrodą dla nas jest także kolejna praktyczna wiedza, która może pomóc rozwiązać problemy z jakością następnemu klientowi.
Zastosowane komponenty
- System wizyjny COGNEX bazujący na algorytmach sieci neuronowych
- Kamery CAM-CIC-5000-20-G firmy Cognex
- Oświetlacze liniowe CCS EL Series
- Dalmierze optyczne PEPPERL+FUCHS
- System zdmuchiwania SMC
- System sterowania Allen Bradley